How to consolidate Blackfabric composites
Blackfabric is the leading manufacturer of thermoplastic prepregs in Spain. Designs, develops and manufactures thermoplastic prepregs at its Barcelona facilities offering a wide range of products and properties.
Thermoplastic prepregs are semi-finished products that are composed of the ideal matrix percentage, ready to be consolidated without additional impregnation processes. These prepregs can be easily consolidated into the desired product through a simple thermoforming process. Thermoplastic prepregs have shorter cycle times during consolidation compared to thermoset prepregs. This attribute enables quicker production rates and increased efficiency. Within minutes, you can create paddle rackets, hockey sticks, trolleys, saddles, instruments, phone cases, steering wheels, helmets, side mirrors, and countless other products. In addition, thermoplastic prepregs can be easily welded and bonded using various techniques, enabling the assembly and integration of complex structures without compromising strength or integrity.
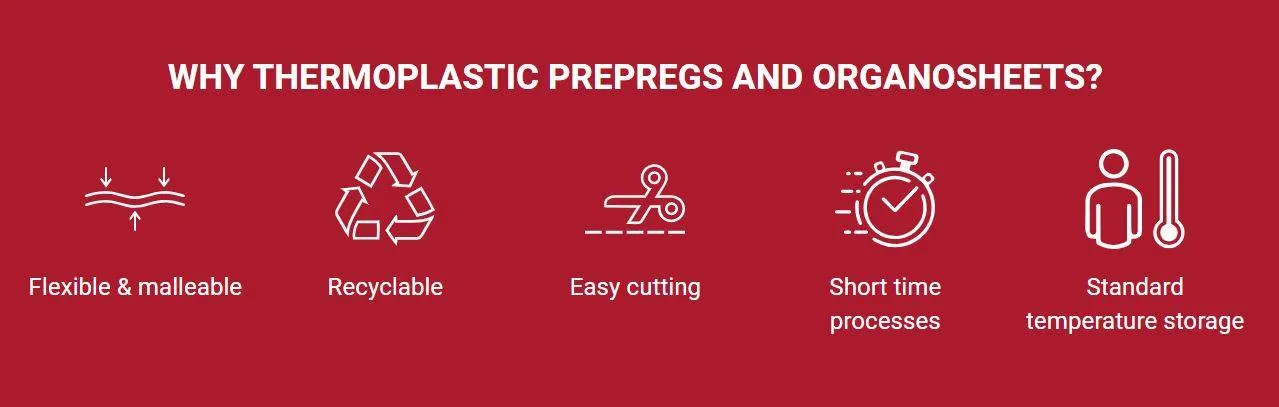
Thermoforming Process Overview
The thermoforming process involves heating the thermoplastic prepreg to its processing temperature, which is above its melting point, and shaping it into a specific form using a mold. Blackfabric prepregs are suitable for various thermoforming processes, allowing flexibility in manufacturing.
Let’s explore four examples of thermoforming processes: compression molding, bladder inflation molding, vacuum-forming, and autoclave consolidation.
Compression Molding
Compression molding involves forcing the prepreg into a mold using a press, typically hydraulically-driven. This process can be either isothermal or non-isothermal.
In isothermal compression molding, the prepreg is placed inside the mold and heated to the polymer processing temperature. Once it reaches the processing temperature, it is left to cool down. Although this process takes longer, it enables the production of complex geometries with low equipment investment. Blackfabric has a hot press specifically designed for isothermal compression molding, which is used for demonstrators, quality control, short series production, and prototyping.
On the other hand, non-isothermal compression molding requires preheating the prepreg before placing it into the mold. This process is much faster and allows for semi-complex geometries.
Bladder inflation molding
Bladder inflation molding is suitable for manufacturing hollow articles like oars. In this process, the prepreg is placed between two clamshells, which are then closed. A bladder is inserted between the clamshells and inflated with air pressure. The mold is heated using a heater or hot dishes. Bladder inflation molding is perfect for producing complex and hollow geometries, making it an excellent choice for low-budget productions.
Vacuum-Forming
Vacuum-forming involves applying heat to the prepreg while creating a vacuum between the mold cavity and the prepreg using a vacuum pump. The vacuum pressure forces the prepreg to conform to the 3D mold, resulting in the desired shape. This process offers relatively fast production, the ability to form large parts, low manufacturing costs, and customizable mold shapes and sizes. However, it is important to note that only one part or article can be made at a time, and achieving very precise details may be challenging. Vacuum-forming is ideal for applications requiring sharper details and molded-in texture, such as automotive parts, fitness equipment, enclosures and covers.
Autoclave Consolidation
Autoclave consolidation is a more advanced and controlled process that involves subjecting the thermoplastic prepregs to elevated temperatures and pressures within an autoclave. This method is particularly effective for high-performance thermoplastics like PC and PPS, as it enables the achievement of excellent consolidation and enhanced material properties. Autoclave consolidation ensures uniform heating and pressure distribution, resulting in parts with superior strength and structural integrity. It is commonly used in aerospace, defense, and advanced engineering applications that require stringent performance requirements.
Conclusion
Blackfabric offers a range of thermoplastic prepregs, including PA6, PC, PP, PPS, PLA, and more, for various composite applications. When it comes to consolidating these materials, customers have several options available, including vacuum bagging, autoclave consolidation, compression molding, and thermoforming. Each method has its advantages and suitability depending on the material and desired part characteristics. Blackfabric’s expertise in thermoplastic composites allows us to assist our customers in choosing the most appropriate consolidation method to ensure the production of high-quality, durable, and precisely shaped composite parts.