Innovation and Precision: Blackfabric’s Laboratory Calender at the Forefront of Technological Projects
Blackfabric is a company in constant evolution, relying on tools that allow it to raise the bar of innovation in the world of composites. This article introduces one of the main tools in the internal laboratory: the laboratory-scale calender.
Research and Development: Advancements Towards Greater Sustainability
In the competitive environment of composites, Blackfabric stands out for its commitment to sustainability and innovation. The focus on thermoplastic prepregs stands out in Blackfabric’s catalog for its advanced recycling capability and high resistance to impacts and fatigue. The laboratory calender is essential for determining the optimal parameters that ensure an effective bond between the thermoplastic matrix and the reinforcement fabrics of the laminated prepregs. This initial process is vital for subsequent scaling to industrial production.
The Laboratory Calender: Precise Adjustment on a Small Scale
The ability to precisely adjust parameters such as speed, pressure, and temperature during pilot tests with the laboratory calender is fundamental. This tool allows Blackfabric’s R&D department to experiment with various combinations of materials, from carbon and glass fibers to natural fabrics such as linen and hemp, using a wide range of thermoplastic films such as PA6, PC, BioPA, or PLA.
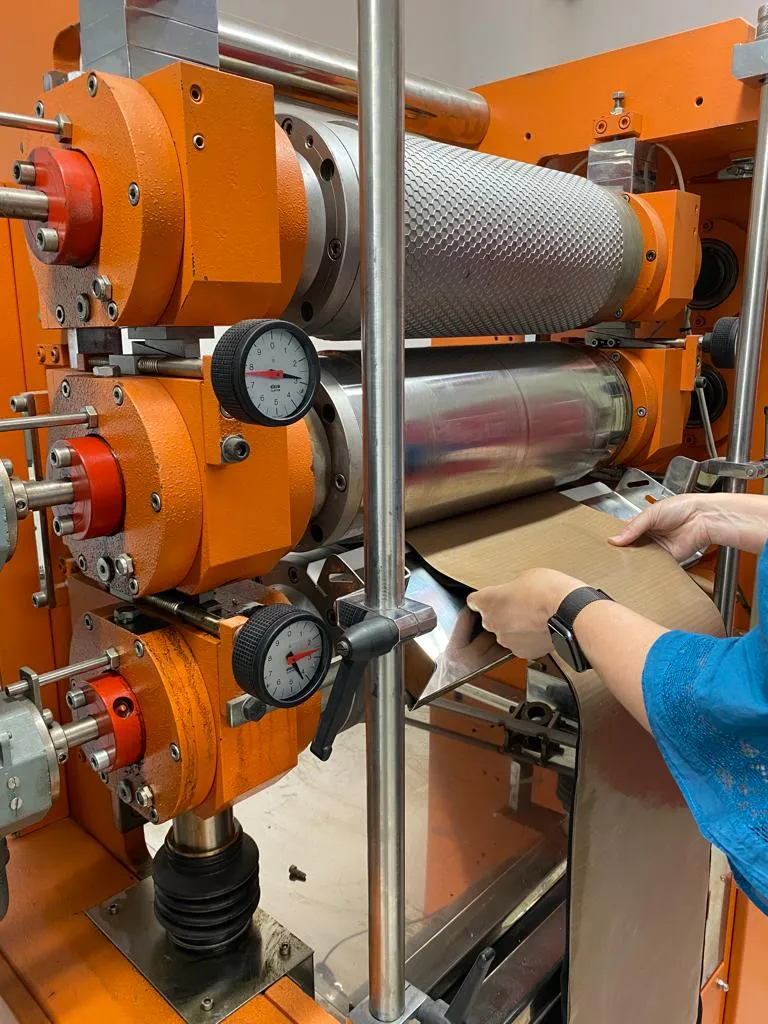
Laboratory scale calender
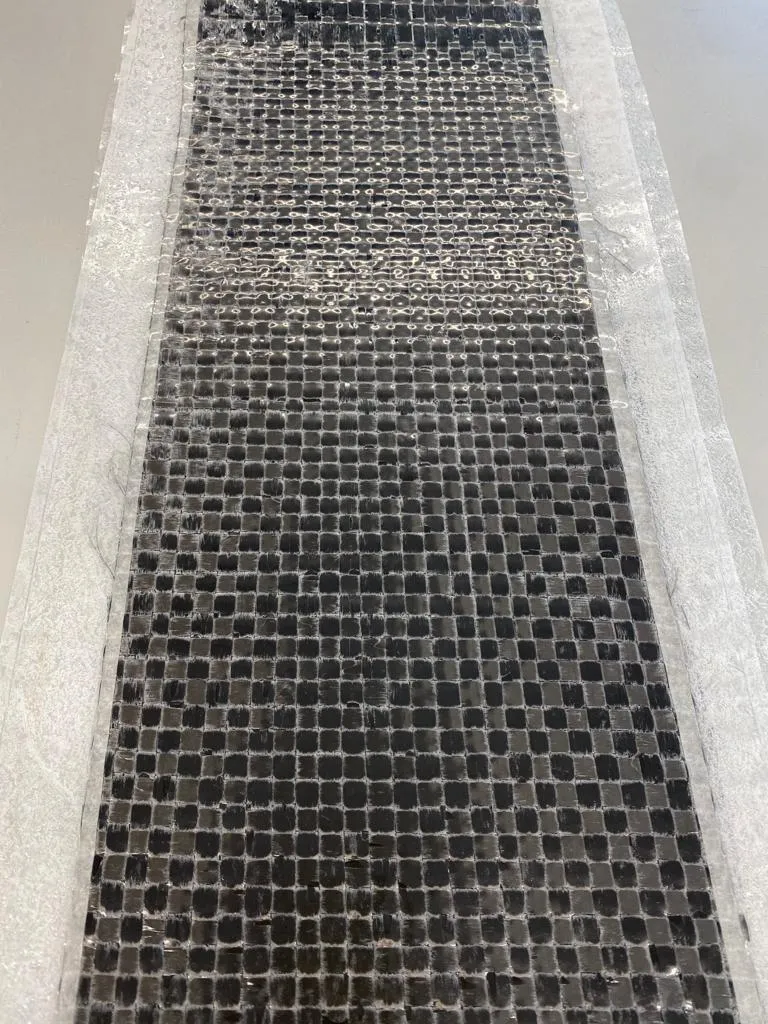
Laminated fabrics
Collaboration and Customization: Adaptation to Customer Needs
Working closely with customers, all kinds of combinations have been tested to meet the specific needs of each application. The laboratory enables testing with multiple combinations of fabrics and matrices, offering customized solutions that meet the requirements of each project.
Specialized Production on the Calender
Blackfabric uses the calender to manufacture two types of articles:
- Stabilized fabrics are produced by laminating a sizing web onto dry fabrics. This process not only facilitates the handling and cutting of fabrics but also significantly reduces fraying problems. The fixing web does not alter the mechanical properties of the final composite material but provides a more manageable and robust structure, allowing for a more efficient manufacturing and handling process. This technique is especially valuable in the production of materials that require high precision and quality in cutting, such as those used in aerospace and automotive applications.
- Prepreg fabrics with film, where a thermoplastic film is laminated on both sides of the reinforcement fabric, resulting in pre-impregnated fabric with thermoplastic matrix, ready to be directly consolidated. These prepregs are ideal for applications where a simple and fast manufacturing process is required, with a very good surface finish.
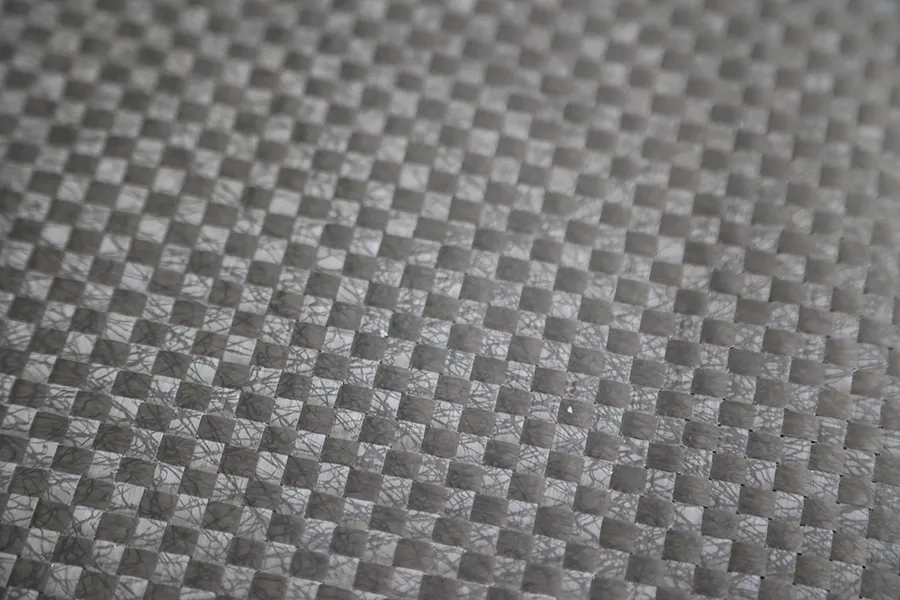
Stabilized fabric
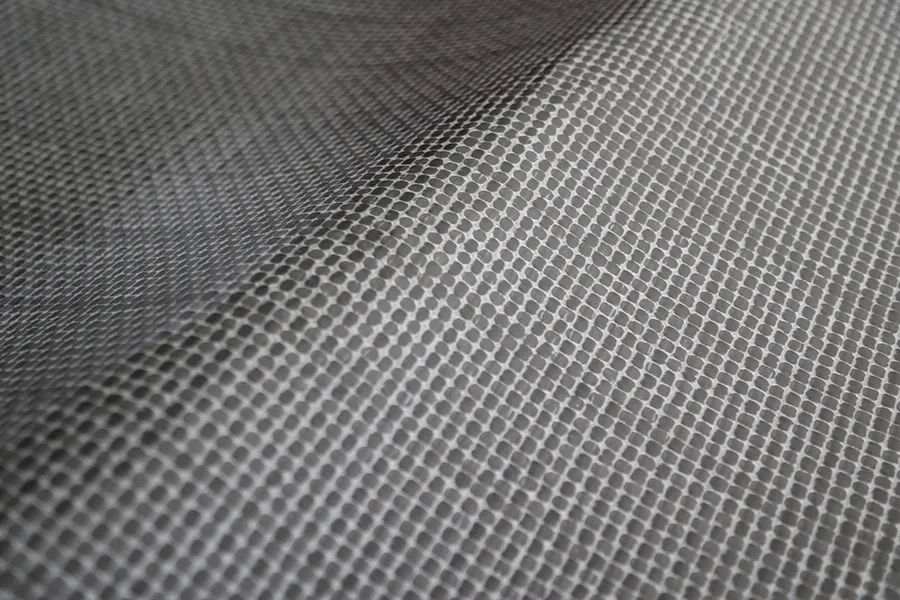
Laminated fabrics
Conclusion: Technology that Makes a Difference
The laboratory-scale calender not only allows for innovation and testing of new products but also supports the development of solutions alongside customers in cutting-edge projects. Blackfabric remains committed to excellence and innovation in every aspect of its work.
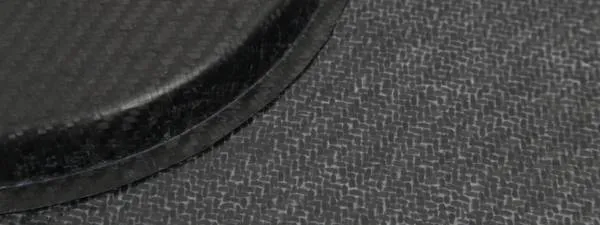
Final appearance after consolidating
Discover the full collection of laminated fabrics offered by Blackfabric in its catalog, and feel free to contact us to develop your customized solution.