New generation of sustainable bidirectional fabrics
Blackfabric has develop a bidirectional fabric made with 100% recycled carbon fibers from recycling pyrolysis processes, together with thermoplastic fibers in a commingled yarn, achieving a thermoplastic prepreg ready to be directly thermoformed.
The impressive growth in carbon fiber consumption in recent years is leading to a significant increase in leftovers and waste being dumped in landfills, as most of the composite materials consumed are not recycled. Environmental legislation is increasingly restrictive with the regulation of this waste and therefore, recycling has become a fundamental and very important issue in all sectors, in terms of limiting the use of finite resources and the enormous need to manage waste disposal. As a result of all these needs, the Blackfabric project emerged to provide more sustainable, recyclable and high value-added solutions in the world of fiber-reinforced materials.
Blackfabric was born from the connection between two Spanish companies from the textile sector, both with more than 20 years of experience in the technical fabrics sector. Marina Textil, is a well-known company in the field of technical fabrics for personal protective equipment, with a production capability of 3.5M meters of fabric and with a sales force to sell fabrics in more than 50 countries around the world. While Texfire is a textile engineering company, which develops customized textile solutions for high temperature applications. Taking advantage of their knowledge in the design and production of technical fabrics, Marina Textil and Texfire have joined forces to launch a new line of evolved fabrics for the world of composites, betting on change, for a more sustainable world.
Blackfabric offers a wide selection of fabrics. Its manufacturing plant is prepared to weave with all kinds of reinforcing fibers and types of yarns, getting final fabrics up to two meters wide. The availability of an in-house bonding plant allows them to introduce polymers on the surface of the fabrics, achieving fiber-reinforced thermoplastic prepregs. Blackfabric focuses mainly on thermoplastic polymers for all the sustainable advantages, improvements in manufacturing processes, time savings and all the added value that thermoplastic matrices provide.
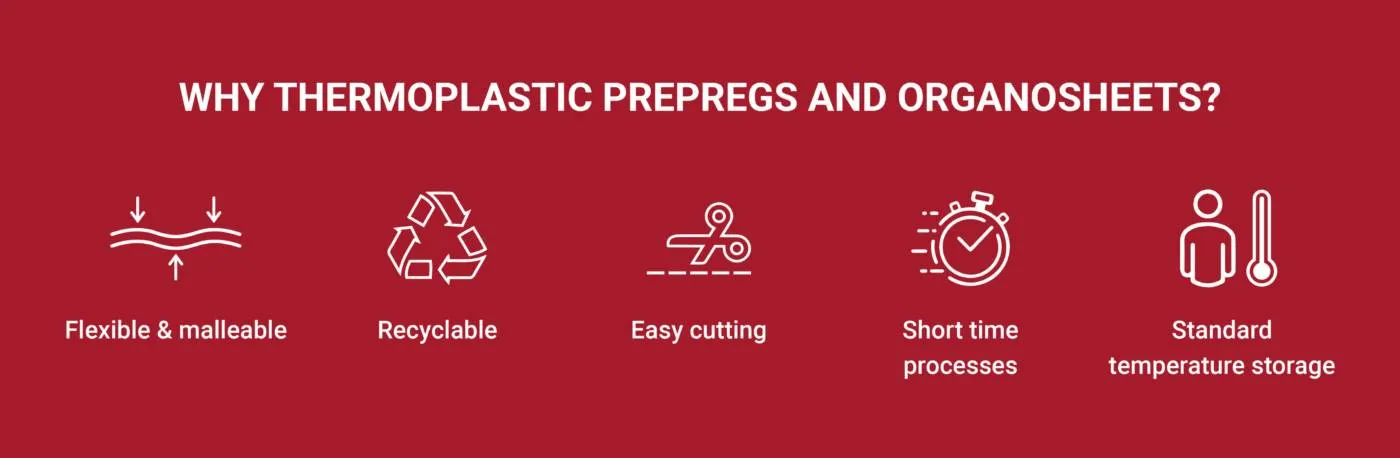
In its production plant, Blackfabric also has a special loom designed to weave with flat wide tapes up to 20mm wide. This has allowed them to design a new collection of bidirectional fabrics produced with tapes impregnated with thermoplastic polymers, also considered thermoplastic prepregs ready to be directly thermoformed. Focusing their efforts on natural fibers, they have developed a bidirectional spread tow fabric, where you can appreciate the yellow-beige color characteristic of linen fibers as well as the technical appearance that wide tapes provide to the final product (picture 2). This fabric is revolutionizing many sectors, and surely will be used in many applications in the next generations.
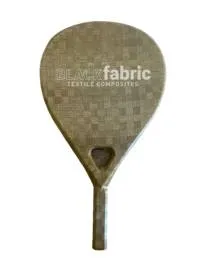
Thanks to the knowledge in weaving technologies and subsequent processes, Blackfabric has been able to take a step forward in sustainable solutions, developing the first high drapability fabric made with 100% recycled carbon fibers.
Discontinuous carbon fibers from recycled pyrolysis processes are oriented together with thermoplastic fibers in a commingled yarn. The composition and properties of the ideal hybrid thread have been defined to achieve a yarn suitable for being woven, which incorporates the right percentage of matrix, obtaining a thermoplastic prepreg, ready to be directly consolidated without need of additional processes.
However, it has been necessary to develop the whole weaving process, adapting the machinery and looms, designing a special space protected from fibrils and dust released by recycled fibers, and adapting the entire production process to the yarn properties.
The resultant bidirectional fabric is apparently similar to a conventional “wool fabric”, very flexible and moldable that adapts well to any geometry. It is easy to cut, manipulate and mold. It can be formed easily, with conventional thermoforming or stamping processes, avoiding additional impregnation processes, neither infusion nor injection, reducing processing times and notably reducing production costs.

In addition, it maintains all the advantages of thermoplastic matrices; easy to store and transport at room temperature, without expiration date, reducing leftovers, with short time processes and with the ability to melt every time the melting temperature of the polymer is exceeded, which allows its repair and recycling of the parts at the end of its useful life.
Visually you can appreciate the patterns formed by the woven taffeta ligament, with the perpendicular threads in 0 and 90º orientation and therefore you can see the alignment of the fibers, something unheard of with all recycled carbon fiber composites known today, where the fibers are randomly distributed without any orientation or order.
The orientation of the fibers and the weaving pattern significantly improve the structural and mechanical properties of the composite. It is evident that the mechanical properties of recycled fibers will not reach the same structural properties as virgin fibers, because recycled fibers are short and discontinuous fibers, while virgin carbon fibers are continuous fibers, a property that is strictly associated with high resistance values that are obtained with materials reinforced with continuous fibers.
Observing the values attached to Table 1, we can determine that Blackfabric’s recycled carbon fiber fabric has mechanical properties below the average mechanical results of virgin carbon fiber thermoplastic composites, but is up to 2 times better than the results. mechanical obtained with non-oriented. recycled fibers.
Table Comparison of mechanical properties
Fabric
Virgin CF/Thermoplastic (general average)
Blackfabric bidirectional fabric Recycled CF / PA6
Non-Oriented Recycled CF / Epoxy Resin
Volum fiber fraction (%)
41%
39%
25%
Tensile Strength (MPa)
700
345
100
Tensile modulus (GPa)
50
31
12
Flexural Strength (MPa)
470
310
–
Flexural modulus (GPa)
48
27
–
This thermoplastic prepreg made with recycled fibers, can be used in many sectors and all those applications where high mechanical strength properties are not required. Like decorative elements, aesthetic parts, body interiors, home accessories, as well as for more functional applications in the world of sports goods and automotive parts, where you can opt for a more sustainable solution, upcycling and giving new life to the fiber recycled carbon.
It is an ideal material for aesthetic pieces, to reflect the ecological values of the company, to involve the customer and to make him feel part of a more responsible and conscious production. The rustic but technical aspect of the fabric allows to reflect the values of sustainability but at the same time is able to provide a high-quality finish necessary to gain the trust of the market and turn it around, starting to bet on recycled fiber materials.
Blackfabric has managed to provide an innovative solution to the recycled fibers sector, improving its mechanical properties, facilitating its handling and use and significantly improving its aesthetics.
The main objective of this development is to motivate all manufacturers of final pieces of aesthetic purpose, opt for this new fabric, for recycled raw material combined with thermoplastic matrices, which will allow the product to be recycled at the end of its useful life.

Finding a new commercial use with recycled carbon fibers Blackfabric contributes to a common good. Upcycling current waste into a new product, revaluing it and re-entering it within the value chain, fostering the circular economy and enhancing recycling is improving significantly the ecological footprint of the company. The fact of being able to give more added value to recycled carbon fibers, thanks to mechanically and aesthetically improvements, making the material usable in multiple applications on the market, can clearly reduce the consumption of raw materials such as virgin carbon, and therefore contributing to all the savings involved.
It is difficult to quantify the environmental impact at this early stage of the project, but it is clear that the use of recycled fibers significantly reduces the environmental impact.
It has been studied that the process of obtaining recycled fibers can reduce the global warming potential by up to 75%, and the amount of energy needed for its production is reduced by 60% compared to the production of virgin carbon fiber, which considerably reduces the carbon footprint of the final product.
In addition, the introduction of recycled carbon fibers into the value chain means that the use of virgin raw materials is reduced exponentially, consequently reducing the waste generated, closing the loop. Exponentially decreasing the manufacture of virgin materials, thus reducing the use of raw materials, and replacing them for recycled materials. All this entails a very important energy and CO2 saving, at the same time as you are adding value to the waste, turning it into a raw material for new products that enter the value chain.
Blackfabric has focused many efforts to develop recycled carbon fibers fabric, and is committed to these sustainable solutions for the common good. They believe that these are the fabrics of the future and claim to this type of advances on technological research to motivate the change gradually to better methodologies, reducing consumption and designing with the circularity of the product in mind, facilitating its recyclability.
The future is upon us, that is why it is essential to start using this type of solutions, and try to start curbing the frenetic environmental impact of the recent years.
MORE INFO : www.blackfabric.eu / contact: info@blackfabric.eu
You can also read the article in the JEC COMPOSITES magazine, edition 146, pages 33-35. We are especially excited to be published in the composites industry’s leading magazine, promoting sustainability and proposing innovative products that can revolutionize the market .
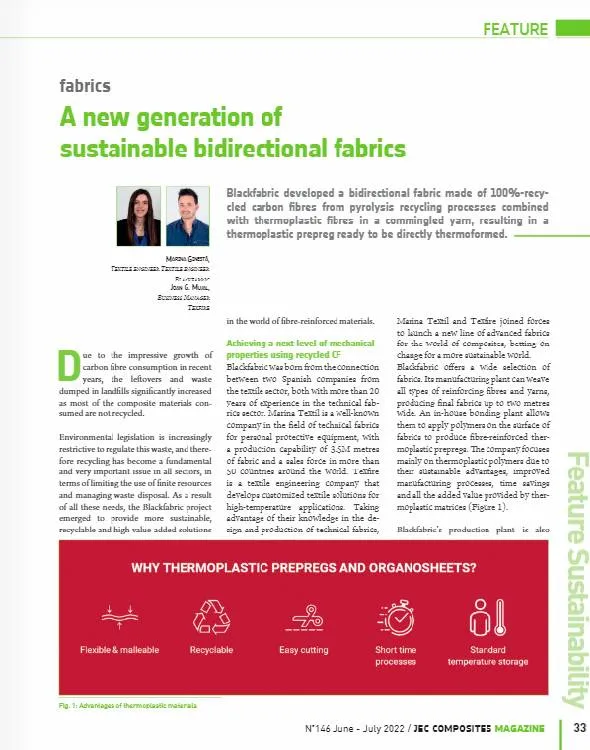
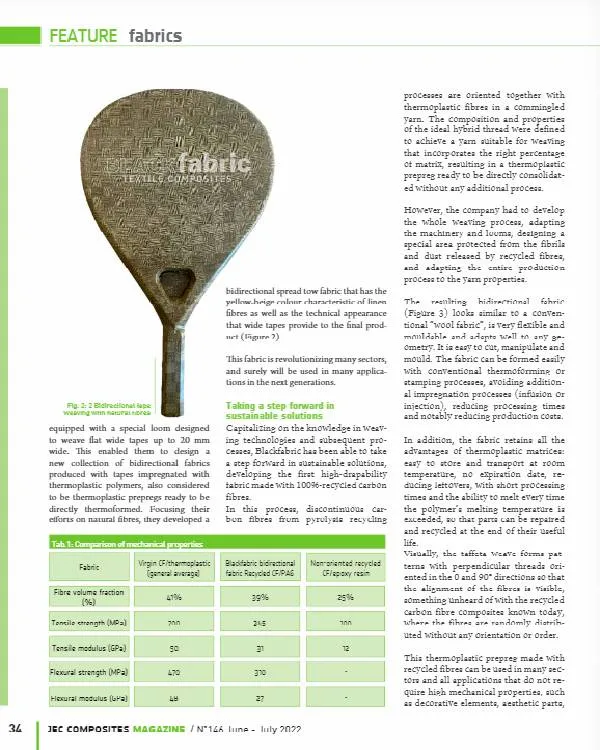
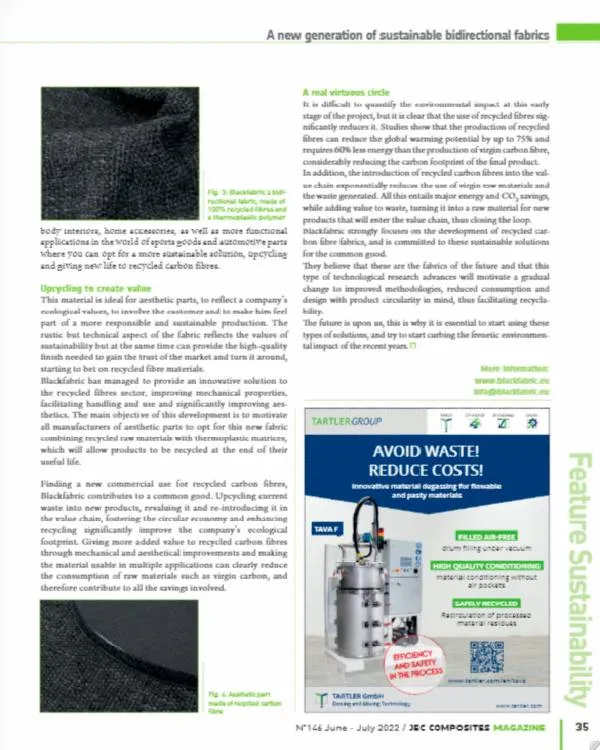